CHEMICAL HYGIENE PLAN
POLICY & PURPOSE
This Chemical Hygiene Plan establishes policies, procedures, and guidelines for chemical safety in all Zoetis Union City work locations.
Colleagues are expected to follow the procedures in this program pertaining to lab and chemical safety, and to adopt safe work practices. Implementing this program is a demonstration of Zoetis Union City commitment to its chemical safety program.
This Plan complies with the OSHA Standard for Occupational Exposure to Hazardous Chemicals in Laboratories (Title 8 CCR, §5191) as it applies to Abaxis’ Research and Development (R&D), Production, Quality Control, and other laboratories.
This Plan also provides guidelines for safe chemical handling in all work areas where chemicals are used and stored, regardless of the type of work area.
The safety measures in this Plan are drawn from a variety of sources, including state and federal regulations, industry guidelines, Fire Code, and to a lesser extent, environmental regulations where appropriate.
Click on each button to learn more or click the switch to open/close all:
RESPONSIBILITIES
Every colleague in the company has an interest in safety. This section includes responsibilities of:
-
Senior Management
-
Managers/Supervisors
-
Safety Officer
-
EH&S
-
Chemical Hygiene Officer
-
Colleagues
SENIOR MANAGEMENT
Supporting the safety program and is ultimately responsible for worker safety. Many work areas follow standard operating procedures that often include safety statements, where applicable.
MANAGERS/SUPERVISORS
-
Incorporating Zoetis Union City safety procedures into their daily activities.
-
Holding training sessions in the work areas on the safe use and storage of chemicals and in any changes to existing handling practices.
SAFETY OFFICER
Informing and training workers in safe chemical handling.
EH&S
Administering and overseeing institutional implementation of the Chemical Hygiene Program (CHP).
CHEMICAL HYGIENE OFFICER
The Chemical Hygiene Officer (CHO) has primary responsibility for ensuring the implementation of all components of the CHP.
Under the OSHA regulation, the CHO is appointed as the lead authority for chemical safety at Zoetis Union City, chosen because of his or her knowledge of the hazardous chemicals used at the site and the processes for using them. OSHA establishes requirements for the CHO and under this standard the responsibilities include:
-
Working with colleagues to develop and implement chemical safety policies and procedures
-
Working with the Safety Committee and EH&S to promote and improve chemical safety, where applicable
-
Working with Zoetis Union City colleagues to resolve and respond to safety issues and colleague concerns arising from the use of hazardous chemicals
-
Assisting with injury investigations, as defined in the Injury and Illness Prevention Plan (IIPP), and aiding in resolving hazardous conditions or unsafe behaviors
COLLEAGUES
Colleagues are responsible for knowing the contents of this Plan and for adopting safe work practices as a primary consideration when performing laboratory tasks or activities in other work areas involving chemical handling. This includes:
-
Planning and organizing tasks in a manner that prevents accidents and exposures to hazardous Materials
-
Following safe chemical handling guidelines, procedures, and policies presented in this and other safety plans
-
Wearing the required personal protective equipment (PPE)
-
Maintaining a workstation that is free of clutter and provides adequate space for safe chemical handling
-
Following procedures for handling hazardous materials, including waste, in a compliant and safe manner
TRAINING
All colleagues who handle and manage chemicals, or who have the potential to work with chemicals, are required to attend Chemical Safety training. Annual update training classes are scheduled as needed or when chemicals and processes involving hazardous chemicals change.
OSHA requires that the training include the following:
-
Methods and observations that may be used to detect the presence or release of a hazardous chemical (such as monitoring conducted by the employer, continuous monitoring devices, visual appearance or odor of hazardous chemicals when being released, etc.)
-
The physical and health hazards of chemicals in the work area
-
The measures colleagues can take to protect themselves from these hazards
-
Specific procedures the employer has implemented to protect workers from exposure to hazardous chemicals
-
The details of this Chemical Hygiene Plan
Supervisors are also encouraged to hold training sessions in the work areas on the safe use and storage of chemicals and in any changes to existing handling practices.
PROGRAM REQUIREMENTS
PRINCIPLES OF CHEMICAL SAFETY
All work areas where chemicals are handled and stored present a risk of exposure or contamination to colleagues if the materials are mishandled or if the workplace is not equipped with adequate control methods.
As a result, the following safety measures have long been considered the cornerstone of laboratory safety:
-
Handle all volatile chemicals in a chemical exhaust hood or under a dedicated exhaust system if a fume hood is not available. Only the R&D and Formulation Labs are equipped with fume hoods.
-
Wear the required personal protective equipment (PPE) for working with chemicals.
-
Maintain a clean and orderly workstation. Keep only the supplies and chemicals needed for that experiment nearby and put them away in an appropriate storage location after use.
-
Substitute a less hazardous material to perform a job rather than one that poses more serious health risks.
Don’t Underestimate the Risks of Chemicals
Many chemicals have more than one risk associated with them. For example, a flammable material can also pose health hazards, as well as being a physical hazard. Even small volumes of chemicals can cause severe injury; therefore, respect for the potential risks is the first step in preventing adverse exposure.
-
Know the hazards of the chemical by referring to the container label or the Safety Data Sheet (SDS). Hard copies are provided in well-marked binders in the hallway outside the Rotor Manufacturing gowning room in Building 1.
-
Avoid complacency when handling chemicals by treating them as hazardous. If the hazards of a chemical are unknown or you are unclear on proper handling practices, make sure that you check the label carefully and the Safety Data Sheet (SDS) for hazard information.
-
Check chemical safety resources on the Internet for specific chemicals.
-
Consult with your CHO or Safety Officer for specific hazard information.
If you have any reason to believe that you or other workers may be at risk of exposure, contact the EH&S department to evaluate the work conditions. Air sampling and personnel monitoring are the only ways to measure chemical concentrations in the workplace.
CHEMICAL HYGIENE PLAN
A written Chemical Hygiene Plan is required to establish procedures, identify control equipment, personal protective equipment and work practices that are capable of protecting workers from the hazards presented by hazardous chemicals used in that particular work place.
This section provides operating practices, procedures, and rules for safely handling chemicals in all Abaxis work areas that apply to this Plan.
This Chemical Hygiene Plan includes the following components:
-
Basic Laboratory Safety
-
Exposure Determination
-
Environmental Monitoring
-
Chemical Procurement
-
Distribution & Transport
-
Storage
-
Housekeeping
-
Safety Equipment & Its Maintenance
-
Risk Control
-
Inspections
-
Medical Program & Surveillance
-
Spills & Releases
-
Exposure Incidents
BASIC LABORATORY SAFETY
The following are basic rules for laboratory safety and have become the standard across all similar industries:
-
Exercise good personal hygiene and wash hands after removing gloves and before leaving the work area.
-
Avoid hand to face contact. Do not apply cosmetics or lip balm, chew gum, or touch your face when handling chemicals, for these activities can transfer contaminants to your face, resulting in a chemical exposure.
-
Only use mechanical or electronic pipetting or mechanical suction methods; never use your mouth.
-
Horseplay is not allowed in the labs, just as it is not permitted anywhere in the facility.
-
Children or pets are not allowed in the lab or manufacturing areas at any time.
-
Wear personal protective equipment that is appropriate to the activity or task.
-
Clean up accidents and spills immediately.
-
Colleagues are instructed to avoid handling highly toxic or otherwise high hazard chemicals while alone in the lab.
EXPOSURE DETERMINATION
Zoetis Unoin City uses the following methods for determining if workers have a potential for exposures to chemicals:
-
Job hazard analyses are developed for all work areas that will determine whether the potential exists where colleague might handle chemicals capable of causing an adverse exposure.
-
Job hazard analyses also provide a practical knowledge of the chemicals used in most work areas, which helps establish safe chemical handling practices for each area.
-
Safe handling procedures are established for particularly hazardous chemicals. For example, organic solvents and volatile materials are used in closed systems, in ventilated enclosures, or in chemical exhaust hoods, where available.
-
Colleagues are instructed in this Chemical Hygiene Plan and in training classes to inform the EH&S department of potential exposure concerns. The work area supervisor or the Safety Officer will arrange for exposure monitoring for particular chemicals to quantitatively evaluate the levels of hazardous materials present in the work area.
-
A process called failure mode effects analysis (FMEA) is conducted for new processes using hazardous chemicals or when a process is changed.
ENVIRONMENTAL MONITORING
Small concentrations of some chemicals are commonly present in labs and Rotor Manufacturing. These are typically controlled by the ventilation and air handling systems specific to that work area. A requirement of this Plan is to evaluate the hazards of a chemical anytime there is a concern that workplace concentrations might pose a risk. Colleague complaints of chemical nuisance or odors must be acted upon quickly to prevent potentially adverse exposures. Zoetis Union City has a legal responsibility to address worker’s concerns and complaints regarding potential risks to health and safety.
OSHA regulates many chemicals with occupational exposure limits, developed to help employers identify whether chemicals are handled in safe concentrations. The only effective means of quantitatively assessing workplace concentrations of chemicals is by conducting quantitative exposure monitoring using a method with validated controls or using protocols authorized by OSHA.
CHEMICAL PROCUREMENT
Purchasing and ordering chemicals is the first stage in planning one’s work with hazardous chemicals. Understanding the properties of the chemicals that you purchase is a key element in deciding the appropriate volume to purchase and in establishing safe handling procedures.
The following guidelines are intended to encourage responsible use of hazardous chemicals from the beginning of the process:
-
Purchase volumes of chemicals appropriate to the work being performed. Buy only what you need, because the costs to manage and dispose of unused chemicals can far exceed the purchase cost by orders of magnitude.
-
If you know that the material will be used, determine if the volumes are appropriate for what Zoetis Union City can store.
-
Ensure there is adequate secondary containment, if necessary, and if the material can safely be transported through the facility with the tools and materials available.
-
Substitute a less hazardous substance for one that is known to be a particularly hazardous material or a select carcinogen. Consider a safer alternative to hazardous agents, if available.
-
Avoid duplicate purchases of chemicals already open and in use. This is important in keeping the inventory of hazardous chemicals under control and saves on unnecessary disposal costs in the future.
-
Place expiration dates on chemicals that can form explosive peroxides after being opened, such as ethyl ether and reactive acids and amines.
SAFETY EQUIPMENT & ITS MAINTENANCE
Safety equipment must be maintained in a manner that will facilitate its effective use in the event of an emergency. The general preventive maintenance program for safety equipment on site includes the following:
-
Chemical exhaust hoods are certified annually. OSHA requires chemical exhaust hoods to operate within a specific velocity range (100-150 linear feet per minute), and are certified annually by a vendor to make sure that the airflow meets this standard.
-
Eyewash fountains and safety showers must be tested periodically as a way of ensuring that clean water is available during emergency use and that an adequate flow rate is maintained according to OSHA standards.
There are two kinds of eye wash stations on site:
-
Faucet Eye Wash stations: These eye wash stations need to be tested weekly where water is allowed to flush for five minutes to verify constant stream and an inspection tag attached to the eye wash station is filled out each time an inspection is performed. The department where the eye wash station is located is responsible to perform the weekly inspection and maintain the eye wash stations.
-
Portable eye wash units: A quarterly service is performed on these eye wash stations by California First Aid. During the service the previous water is drained and refilled with fresh water and an additive is added to prevent the growth of bacteria.
Colleagues are encouraged to inspect equipment periodically and report any problems to the area supervisor or EH&S department so it can be repaired as soon as possible. Defective equipment can result in serious consequences so it is incumbent on the users to take potentially unsafe equipment out of service until it can be repaired or replaced.
DISTRIBUTION & TRANSPORT
Hazardous materials used in Manufacturing and Product Development are delivered in Receiving and taken to an interim quarantined storage cage until QA releases them. Receiving staff should look for leaks, damage to containers, and other signs of possible damage to the container that may result in contact with the chemical. If the package is damaged, set it aside and contact the EH&S department for guidance on the proper handling.
Chemicals for R&D are received and delivered to the R&D lab. Once received, chemicals are put away in an appropriate storage location as soon as possible. Flammable materials should be unpacked into a flammable storage cabinet. Acids and bases are stored in an appropriate corrosives storage cabinet.
All chemicals must be safely transported through the building using a cart with a safety lip to prevent spills and accidents. Avoid carrying packages that obstruct visibility or packages that are heavy enough to warrant the use of a cart. If transporting hazardous chemicals in the building, such as 4-liter solvent bottles, use a solvent carrier, a lab tray, or tub to prevent spills and releases.
Chemicals are not to be transported in carpeted areas or through administrative parts of the company. Chemicals must never be delivered to offices or cubicles.
CHEMICAL STORAGE
Chemical compatibility determines the appropriate storage location. For example, flammable and combustible chemicals are best suited for storage in an approved flammable storage cabinet, while acids and oxidizers should be stored separately to prevent 2 incompatible chemicals from potentially contributing to a hazardous condition.
Never store incompatible chemicals together. Use SDS’s to determine the appropriate hazard classes.
Chemicals are classified into hazard classes, each requiring separation from other chemical classes during storage. This hazard classification is used to separate incompatible chemicals and to prevent their potential for mixing together, which can result in the production of toxic vapors, heat-producing reactions, or the generation of byproducts more toxic than the original chemicals. Seismic safety and chemical compatibility are important considerations when storing chemicals based on hazard class.
The following tips on proper chemical storage:
-
Acids and bases - If these are stored in the same cabinet, the volatile acid gases react and form dust films on surfaces. On the other hand, ammonium hydroxide, a strong base, produces ammonia vapors, which should not come in contact with acids.
-
Flammables and oxidizers - These are more difficult to identify, so consider most, if not all, organic solvents and flammable solids to be potential fuels for a fire. Store organics away from oxidizing gases and liquids (e.g., oxygen and hydrogen peroxide solutions, organic peroxides, nitric and sulfuric acids).
-
Water-sensitive materials – They should be stored in cool, dry places or in desiccators with a good seal on the lid to prevent them from getting ruined. Examples include metal hydrides (lithium aluminum hydride, organic peroxides) or elemental metals such as sodium or lithium.
-
Shock, light, or heat-sensitive materials - Store such reagents and other reactive materials in cool, dry, dark places. This category includes ethers and organic solvents that are capable of forming explosive peroxides. These materials must have an expiration date written on the container when they come on-site, which must be considered in addition to following proper storage conditions. This helps identify if the material is susceptible to instability and hence, explosiveness.
Fire Code requires that incompatible chemicals be segregated from each other by a 50-foot distance, or in separate secondary containers. Chemical storage locations should have a shelf restraint or be stored in secondary containment to capture the material if it is spilled. This applies to hazardous waste as well as chemical products.
Avoid storing chemicals on the bench or in fume hoods in order to maximize space to safely handle chemicals and to prevent clutter, which contributes to accidents and releases. Instead, put chemicals away after use or at the end of the work shift. Opened bottles produce vapors, thus adding to the importance of storing them where vapors cannot accumulate or present a risk of exposure, fire, or spills.
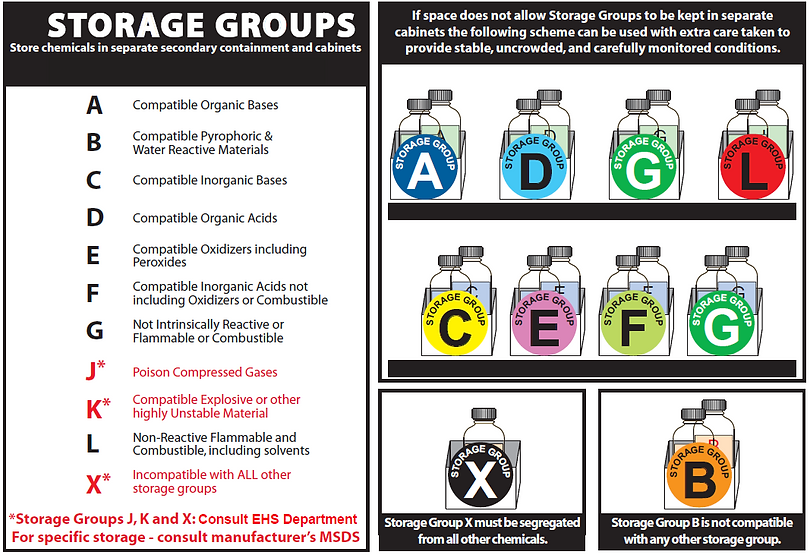
HOUSEKEEPING
Stage only the chemicals that are needed for your daily work in the immediate work area, and provide adequate room for safely conducting work. The following are common rules for work areas involving chemicals:
-
Put chemicals away after use or at the end of a work shift as a preventive measure against accidental spills and releases.
-
Include seismic safety considerations to ensure that chemicals do not present a risk in the event of a strong earthquake.
-
Avoid cluttered and messy workstations that reduce the space colleagues can safely conduct work.
-
Colleagues are expected to clean bench surfaces each day after finishing work in that space. Even small quantities of some hazardous chemicals can become a health risk from residues left behind.
-
Store chemicals and chemical formulations of all kinds on the lowest shelf as a way to prevent injuries from falling bottles and spilled chemicals during an earthquake.
-
Equipment and supplies should not be left on the floor or in high traffic areas and empty boxes should not be accumulated.
-
Avoid storing supplies and waste containers in the knee spaces underneath the benches. Stockpiled equipment and supplies can block exit paths and reduce safe refuge for workers during and after an earthquake.
CHEMICAL RISK CONTROL
The Zoetis Union City applies a 3-tiered hierarchy when evaluating the control of hazardous chemicals in the workplace using one or more of the following control methods. The 3 tiers include:
-
Engineering Controls.
-
Administrative Controls (also known as Work Practice Controls).
-
Personal Protective Equipment (PPE).
ENGINEERING CONTROLS
Any device or piece of equipment that separates the user from the chemical is considered an engineering control.
Engineering controls include ventilation and exhaust systems, such as fume hoods or dedicated exhaust hoods and enclosures used to separate workers from the hazard. Engineering controls are at the top of this hierarchy because they are more reliable than other methods for controlling contaminants at the source of generation.
Good ventilation is one of the key elements in preventing occupational exposures, because air movement prevents the accumulation of contaminants that may occur in some areas. Exhaust systems for controlling chemicals must be separate from the “house” system, which ventilates administrative areas. This ensures that in the event of a release, hazardous chemicals do not affect workers outside the labs and manufacturing areas.
Appropriate ventilation for the hazards being handled is one of the most important elements to preventing exposure to hazardous materials. In work areas where the handling of hazardous chemicals occurs without dedicated ventilation, reduce the handling to short periods of time to prevent exposures.
Most work areas at Zoetis Union City have sufficient air movement so small amounts of most chemicals do not pose a risk. The risk increases if these chemicals accumulate without being adequately removed from the workplace atmosphere. Building ventilation systems must be appropriate for the type of work being conducted in the labs, manufacturing areas, and warehouses, and must not contribute to the accumulation of chemical vapors.
In general, ventilation in areas where hazardous materials are handled should create a negative air pressure to ensure that air is directionally exhausted away from corridors and common work areas. Air handling systems in clean work locations, such as Manufacturing, may create a positive directional airflow in order to protect the product.
Standard practices for controlling hazardous vapors include the following:
-
Chemical storage areas and waste accumulation areas should be well ventilated to prevent accumulation of vapors produced by open chemical containers.
-
Volatile or flammable chemicals must be kept closed when not in use.
-
Exhaust devices specific to a workstation must meet acceptable performance standards and adequately remove harmful chemicals.
-
OSHA requires that chemical exhaust hoods operate at between 100–150 linear feet per minute (lfpm) and are certified annually by a third party to verify proper operations. OSHA also requires that an air velocity meter or alarm is installed on all fume hoods.
-
Laboratories air handling systems must be separate from administrative and common areas to prevent chemicals from entering in the public ventilation.
Ventilation controls on site include the following:
-
Chemical fume hoods in the R&D and Formulation labs
-
Small fans used to control lead fumes from soldering operations in Instrument Manufacturing
-
Exhaust lines in the machine shop are connected to machines where combustible dusts and metal filings are produced
ADMINISTRATIVE CONTROLS
If engineering controls are not solely effective or feasible in controlling contaminants, then it may be necessary to establish procedures or specific work practices to minimize the potential for exposure to chemicals. Administrative Controls (also known as work practice controls) utilize safe work practices and procedures that are built into a task or activity, some of which are discussed in the previous sections of this Plan.
Examples of administrative controls include the following:
-
Hazardous Materials storage practices and locations that prevent spills or exposures to hazardous materials
-
Waste handling methods that prevent breathing hazardous vapors or other contact with waste
-
Safe transport of hazardous materials by using secondary containment or carts to prevent spills and accidents
-
Preventive maintenance program
-
Good housekeeping
-
Good personal hygiene
-
Effective decontaminating procedures
-
Storing liquids off of the floor or in secondary containment, if floor storage is unavoidable
-
Using proper storage and waste containers
Administrative controls must be incorporated carefully if applied to the control of hazardous chemicals, and should be evaluated by a safety professional to ensure that workers are not at risk.
PERSONAL PROTECTIVE EQUIPMENT
If administrative or engineering controls or both are not adequate in controlling workplace contaminants, then it may be necessary to provide personal protective equipment (PPE) to protect colleagues from residual chemical hazards.
The safe handling of chemicals, and particularly hazardous chemicals, requires at a minimum the following PPE:
-
Lab coat or smock in Manufacturing, R&D and QC labs
-
Chemical-resistant gloves – nitrile, latex, vinyl, neoprene, etc.
-
Safety glasses or goggles
-
Closed-topped shoes
-
Face masks (depending on location)
INSPECTIONS
The Injury and Illness Prevention Plan requires that periodic workplace inspections include the safe use and storage of chemicals, and assess safety procedures, policies, and guidelines as set forth in this Plan and other manuals.
Inspections by state and local regulatory agencies are also conducted periodically. The local fire department conducts fire code inspections each year, while the Union City Environmental Health Division conducts inspections of hazardous materials and hazardous waste handling practices.
MEDICAL PROGRAM & MEDICAL SURVEILLANCE
First-aid kits are provided for workers when they sustain minor injuries such as cuts, scrapes, or superficial wounds. First-aid kits are located in the break rooms, in anterooms to Rotor and Bead Manufacturing, as well as in other strategic locations in the throughout our buildings.
OSHA Select Carcinogens require that employers establish a basis for ensuring that colleagues are not exposed above legal limits.
Any colleague who suffers a chemical exposure is sent to the clinic for observation and treatment. The health care provider can help answer questions and establish a medical monitoring program for select chemicals, if necessary.
In the event an adverse exposure occurs from any workplace chemical, colleagues must be provided with appropriate medical attention after the exposure occurs, including confidential medical surveillance, guidance, and advice while being treated.
Human Resources must retain medical records from exposures and occupational injuries for the duration of a colleague's employment plus 30 years.
SPILLS & RELEASES
Chemical spills and releases require immediate attention to prevent exposures to personnel and contamination of surrounding surfaces.
HAZARDOUS MATERIALS EXPOSURES
Exposures to hazardous chemicals can be severe and should be handled quickly to prevent injuries from such exposures. In all cases, medical follow up must be provided for all chemical exposures.
RECORD KEEPING
All health and safety training records are maintained by EH&S for 3 years.
Medical records are maintained by HR for the duration of the worker's term of employment plus 30 years.
CHEMICAL WASTE MANAGEMENT
The Environmental Health and Safety function at Zoetis Union City manages chemical waste, including contracting with vendors, establishing waste profiles, managing waste manifests, and working with waste generators to comply with all applicable regulations. This section applies only to workers who have been designated to handle Chemical Waste.
WASTE LABELING
All chemical waste containers must have a hazardous waste label placed on the container as soon as waste begins to be collected. Labels must be specific to the waste stream and the date must be filled in each time waste is emptied from the container. Labels for multiple hazardous waste streams are available at EHS department.
Hazardous waste labels are available from EH&S and in the Hazardous Waste Accumulation Room (HWAR) of Building 1. Here is an example label:

HAZARDOUS WASTE STORAGE
Hazardous waste is accumulated in the Hazardous Waste Accumulation Room (HWAR) until the vendor picks it up. Locations where waste is collected at the point of generation are called Satellite Accumulation Areas; these allow waste to be stored for longer periods of time than the HWAR accommodates. Access to the HWAR is restricted to only properly trained workers. The conditions for storing hazardous wastes include:
-
Keep waste containers closed.
-
Keep outsides of container clean.
-
Make sure containers are free of defects. Contact EH&S if a defective container is discovered.
-
Never fill containers to the very top. Leave 3 inches from the top of the container in drums and 1 inch for small containers.
-
All liquid waste containers must have a secondarily means of containment.
-
Secondary containers must be free of spills and residues.
-
All waste containers must be properly labeled.
-
All hazardous waste in the HWAR must be disposed of within 180 days from the accumulation start date. Satellite Accumulation Areas are permitted to store waste for up to one year.
-
Incompatible wastes must be segregated using secondary containment.
CHEMICAL WASTE STREAMS
Zoetis Union City currently generates multiple chemical waste streams, with the most common waste streams listed below.

These waste streams are characterized for an appropriate disposal method by completing a vendor’s Hazardous Waste Profile, as indicated below. The disposal facility must approve the waste profile annually, and new chemical constituents require a revised profile. Labels for these waste streams are available in the HWAR. If you have a waste stream that is not listed in this table, notify EH&S.
Step-by-Step Instructions for transporting and collecting these waste streams in the HWAR are provided during Hazardous Waste Handler Training and are detailed in a Training Binder in the HWAR.
HAZARDOUS WASTE HANDLER TRAINING
All colleagues who generate, handle, transport, or are otherwise involved in hazardous waste management must attend training and annual refresher training. Colleages that are assigned to handle waste prior to the next available training may receive temporary access to the HWAR as long as they are accompanied by a trained colleague who walks them through the training binder in the HWAR.
UNCOMMON CHEMICAL WASTE - LABPACK
It is very important to add only the specified waste constituent to a designated waste stream.
Small quantities of chemical waste, unwanted chemicals, expired chemicals, or any other chemicals which are not part of a designated waste stream are disposed of in a LAB PACK. These items have a LABPACK profile created specifically for this disposal event.
Items for LABPACK must be labeled, logged on a LABPACK list in the HWAR, and placed in the bin found there. Colleagues must contact and inform the EH&S representative before transporting LABPACK waste to the HWAR.
If a worker is not sure how to handle or dispose of any chemical or chemical waste, he/she should consult with the EHS department.
Empty Liquid Containers
-
Liquid containers of 5 gallons or less may be disposed of in the trash.
-
Containers that are larger than 5 gallons must be marked with the date they were emptied and must be disposed of within one year of being empty. The waste vendor will help dispose of these larger containers.
-
The labels of empty liquid waste containers must be defaced using an indelible ink. Then the container can be disposed of with waste. Deface the label with permanent black marker by drawing a single line through the label, writing the word “EMPTY” in all caps and the date.
-
Avoid placing glass bottles in garbage bags because the glass can break and cause injury to those disposing of them.
Empty Solid Waste Containers
-
Deface the label of empty hazardous material container using permanent black marker as indicated above and dispose of it in the trash.
OTHER HAZARDOUS WASTE STREAMS
Batteries
Lead acid, alkaline, and lithium batteries must be insulated from each other and have terminals protected by clear tape or placed in sealed plastic bags to prevent short circuit in accordance with 49 CFR 172.102, Special Provision 130 and 173.159. Dry cell batteries rated at more than 9V must also be insulated in the same manner. Duct tape may not be used. Batteries may not be connected in series to one another.
Alkaline, lead acid, lithium and dry cell batteries must be separated by type and collected in different containers. Appropriate universal waste labels must be affixed to each container and the collection start date must be documented on the label.
Universal Waste
-
Universal waste consists of electronic waste that must have its hazardous components removed or recycled before disposal in the municipal landfill.
-
Consult with the IT Department for disposal of Zoetis/Abaxis-issued electronic devices.
-
Fluorescent light bulbs are collected in cardboard boxes and drums in the HWAR and disposed of by the vendor.
PERSONAL PROTECTIVE EQUIPMENT
Colleagues who handle hazardous waste are required to wear appropriate personal protective equipment (PPE). At a minimum, colleagues must wear appropriate protective gloves, safety glasses when splashing may occur, and closed-topped shoes.
Nitrile gloves should be worn when handling chemical waste because those gloves are the most protective and do not permit chemicals to penetrate the glove.
REFERENCES
VIDEOS
eLEARNING
DOCUMENTS/LINKS
-
29 CFR 1910.151 OSHA Requirements for Emergency Eyewashes and Showers
-
ANSI [Z] 358.1-2004 ANSI Standard for Emergency Eyewash and Shower Equipment
-
TITLE 8 CCR, §5191 OSHA Standard for Occupational Exposure to Hazardous Chemicals in Laboratories
-
CA FIRE CODE Hazardous Materials Section 49 CFR 172.102, Special Provision 130 and 173.159
-
CFR 1910.120 - Hazardous waste operations and emergency response
SUPERVISOR & SAFETY LEADER DEEPER DIVES
GLOSSARY
Action level (CHEMICALS)
Chemical Hygiene, HazCom
A concentration designated for a specific substance, calculated as an eight-hour time weighted average, which initiates certain required activities such as exposure monitoring and medical surveillance. The action level is always lower than the corresponding Cal/OSHA permissible exposure limit (PEL) and is designed to protect personnel from overexposure.
Acute toxicity
Chemical Hygiene, HazCom
Acutely toxic substances cause adverse effects by any of the following exposure methods: Oral or dermal administration of a single dose of a substance. Multiple oral or dermal doses within a 24-hour period An inhalation exposure of 4 hours.By the criteria listed below, substances are placed in one of four toxicity categories according to their experimentally derived LD50 or LC50 values.
Administrative Controls
Chemical Hygiene, BBP, Biosafety, HazCom
Controls include limiting the length of time an employee is exposed to hazardous atmospheres.
Asphyxiant
Chemical Hygiene, HazCom
See simple asphyxiant
Aspiration hazard
Chemical Hygiene, HazCom
A liquid or solid chemical that causes severe acute effects if it infiltrates into the trachea and lower respiratory tract. Possible effects include chemical pneumonia, pulmonary injury, or death.
Boiling Point
Chemical Hygiene
The temperature at which the vapor pressure of a liquid equals the surrounding atmospheric pressure. For purposes of defining the boiling point, atmospheric pressure shall be considered to be 14.7 psia (760 mm Hg).
Carcinogen
Chemical Hygiene, HazCom
1) A substance is considered to be a carcinogen if: (a) It has been evaluated by the International Agency for Research on Cancer (IARC) Monographs and found to be a carcinogen or potential carcinogen; or (b) It is listed as a carcinogen or potential carcinogen in the Sixth Annual Report on Carcinogens published by the National Toxicology Program (NTP) or, (c) It is regulated by Fed/0OSHA or Cal/OSHA as a carcinogen
2) A substance or a mixture of substances which induce cancer or increase its incidence. See also: Select Carcinogen
Classification
Chemical Hygiene, HazCom
To identify the relevant data regarding the hazards of a chemical; review those data to ascertain hazards associated with the chemical; and decide whether the chemical will be classified as hazardous, and the degree of hazard where appropriate, by comparing the data with the criteria for health and physics hazards.
Combustible Liquid
Chemical Hygiene, HazCom, Fire, Emergency Response
Any liquid having a flash point greater than 93C (199.4F).
Combustible Liquid
Chemical Hygiene, HazCom, Fire, Emergency Response
A combustible liquid shall be defined as any liquid that has a closed-cup flash point at or above 100F (37.8C). (a) Class II Liquid. Any liquid that has a flash point at or above 100F (37.8C) and below 140F (60C). (b) Class IIIA Liquid. Any liquid that has a flash point at or above 140F (60C) but below 200F (93C). (c ) Class IIIB Liquid. Any liquid that has a flash point at or above 200F (93C).