POWERED INDUSTRIAL TRUCK SAFETY
POLICY & PURPOSE
It is Zoetis Union City policy that all colleagues who operate a powered industrial truck or powered industrial lift truck (PIT) receive adequate training and demonstrate competency in the safe use of the powered trucks that are assigned to each work area.
This Plan establishes policies, safe work practices, and procedures for a safe and compliant lift truck (forklift) and powered truck program.
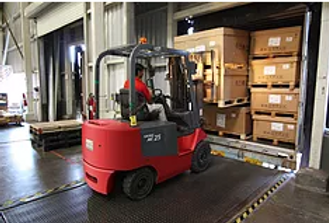
This Plan is based on OSHA requirements for Industrial Lift Trucks (Title 8 CCR, Article 25). This Plan provides the standards by which forklift safety is managed in all Zoetis Union City facilities and is intended to provide guidance and serve as an informational resource for forklift users.
Click on each button to learn more or click switch to show/hide all:
TRAINING
OSHA requires that workers attend initial Forklift Safety training for new operators, and refresher training at least every 3 years. Zoetis Union City requires that all colleagues who operate a lift truck or powered truck of any type are trained and show competency in the safe handling of a vehicle before being allowed to use one. There are 3 basic components to safety training, which include the following:
-
Formal instruction such as a lecture, discussion, interactive computer learning, videotape, and written material.
-
Practical training which includes hands-on demonstrations by the trainer and exercises by the trainee on the model of forklift or powered truck the colleague will use.
-
An evaluation of the effectiveness of the training by observing the operator’s performance while doing actual work using the forklift.
In addition, refresher training must be given if the operator has been involved in an accident, near miss, or unsafe operations.
OSHA requires that the following topics be discussed in training:
-
Operating instructions
-
Vehicle controls and instrumentation
-
Engine or motor operation
-
Steering and maneuvering
-
Fork and attachment adaptation, operation and use limitations
-
Vehicle capacity
-
Vehicle stability
-
Vehicle inspection and maintenance
-
Refueling and/or charging and recharging of batteries
-
Operating limitations
-
Warnings or precautions in the operator's manual
If an operator is assigned to a new type of forklift, or if workplace conditions change that could affect safety, then refresher training is required. Training covers the principles of forklift safety and the practices and procedures specific to the work area and to the forklifts used.
PROGRAM REQUIREMENTS
Types of Lift Trucks
Zoetis Union City uses electric-powered forklifts, propane powered forklifts, and powered pallet trucks in the Shipping and Receiving Departments. We also have one our more battery powered utility carts for transport between Building 4 and Buildings 1&2. All powered trucks are maintained by Shipping and Receiving staff or an outside vendor. The following sections describe the types of lift trucks used at our site.
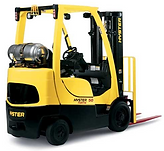
Counterbalanced Forklifts
Zoetis Union City uses propane-powered rider trucks in the warehouse that are counterbalanced with weights. These units require the operator to be seated in a cage with an overhead guard and are intended for one operator. These forklifts are rated at a maximum of 3,450 pounds, which is based on the weight of the counterbalance. They are equipped with solid tires, thus are intended for indoor use. The forklift trucks we use have 3 stages on the mast.
Unlike a car, the rear wheels steer the forklift in a tight turning radius, while the front wheels are designed to drive it. The counterbalance is usually several thousand pounds in weight and is designed to offer stability when handling loads in both vertical and horizontal directions

Powered Pallet Jacks
Among the type of powered pallet lift trucks Zoetis Union City uses are high-lift units, which are equipped with a high-lift mast, useful for reaching high shelves on racking systems. The high-lift trucks are designed with 2 “outrigger” wheels in front that allow the forks to straddle a pallet and serve to add stability because these units do not have a counterbalance. They have a lower-rated capacity, and are intended for lighter loads in small or constrained warehouses.

Powered Utility Carts
The Bigfoot powered utility cart is used for deliveries between Buildings 1, 2 & 4. Although this vehicle is similar to an automobile, specific training is required to operate this cart as improper operation can result the cart becoming unstable and potentially tipping over causing serious consequences for the operator.
The Principles of Forklift Safety
There following 4 principles of lift truck safety work together to form the basis of safe operations. These are basic principles of physics related to stability and centers of gravity, as the following section discusses.

1) Fulcrum Point and Load Center
The forklift is like a lever, with the center of balance, or fulcrum point, located directly under the front wheels of a counterbalanced forklift. The fulcrum point does not change, regardless of the size of the load. If the load is heavier than the counterbalance, the forklift will tip forward. However, a light load will not tip the forklift backwards, because the weight is distributed across the length of the forklift, making it stable at rest.

2) Load Capacity and Load Rating
All lift trucks have a capacity plate that indicates the manufacturer’s recommended weight of a load the lift truck can safely handle. The rated capacity is based on an evenly distributed load center that is at least 24 inches from the heel of the forks.
Load capacity can change depending on the following:
-
Distance of the load center from the forks.
-
The height of the load.
-
The location of the load center
The operator must assess the weight and center of gravity (aka load center) of a load before trying to lift it. This ensures that the forklift is able to perform the job. The operator must then also assess how best to move the load and establish a safe center of gravity for both the load and the forklift.
Awkward or odd-sized loads may require extra thought as to the location of the load center, and how best to move them, because off-centered loads cause the load and the lift truck to be unstable.

3) Stability and Center of Gravity
The forklift has a center of gravity, just as the load has one. The primary difference is that the forklift’s center of gravity changes with a load as the load is raised or shifted sideways. When the forklift is at rest, the center of gravity is underneath the driver’s seat. When the load is lifted, then a “combined center of gravity” is created, which is based on the following factors:
-
Size of load
-
Weight or load
-
Shape of load
-
Position of the load
The combined center of gravity also changes depending on the tilt of the forks because it changes the load center. The most stable position of the forks is when the load rests against the backrest and the forks are tilted slightly back. When the mast is tilted forward the combined center of gravity moves toward the front of the forklift, making it front-heavy. Forks must only be tilted forward when picking up or dropping a load.
“Load center” means the center of gravity of the load. The load center is typically measured from the heel of the forks to the center of the load. The closer the load center is to the backrest, the more stable the load. As the load center moves away from the heels of the fork, or backrest, the capacity of the forklift decreases. For every inch away from the heel of the forks, the rated capacity will decrease by 100 pounds, which also moves the center of gravity further away from the counterbalance, reducing stability.

4) The Stability Pyramid/Triangle
Drawing a line between the front wheels and the center of the rear axle forms an imaginary triangle, called the stability triangle. At rest, the center of this stability triangle is underneath the driver’s seat, which is discussed above as the forklift’s combined center of gravity with no load or while at rest. As a load is lifted, the triangle turns into an imaginary pyramid and the combined center of gravity rises through the center of the pyramid. As the load rises, the stability pyramid, or stable range, becomes narrower and taller.
If the load’s center of gravity moves outside the stability pyramid, the forklift will fall over. Other forces, such as driving too fast, making sharp turns, braking hard, or moving a load with elevated forks, will contribute to a loaded forklift falling over.
Operator Safety Rules and Procedures
The following rules are considered standard industry practice and are intended to reduce the risk of overturn accidents, collisions, loss of the load, or injury to others:
-
Wear the seat belt at all times when operating a forklift.
-
Make sure the load is stable and safely arranged on the forks.
-
Do not tilt the forks forward except when picking up or depositing a load.
-
Tilt the load backward only enough to stabilize the load.
-
When traveling keep the load low, just above the pavement, with forks tilted back to maximize stability.
-
Enter truck trailers squarely and not at an angle.
-
Keep the load uphill when going up or down an incline or ramp.
-
Drive at a speed that will allow you to stop safely within the stability triangle.
-
Slow down on wet or slippery surfaces.
-
Slow down to make turns.
-
Avoid driving over loose objects or on surfaces with ruts and holes.
-
Drive in reverse if the load blocks the view.
-
Lift the forks only when ready to place or lift a load.
-
Avoid driving along the edge of a loading dock and always face the open door.
Traveling
The basic premise for traveling is that you maintain control of your forklift at all times.
Other rules include the following:
-
Operate a forklift only while in the seat or operator’s station. Never start it or operate the controls while standing beside the forklift.
-
Never allow passengers.
-
Do not put any part of your body between the uprights of the mast or when traveling, outside of the forklift frame.
-
Always look in the direction of travel and keep in reverse if the load blocks your view.
-
Always observe posted speed limits at your workplace. A forklift should not be driven faster than a quick walking pace.
-
Keep a distance of at least 3 forklift lengths between you and any forklift traveling in front of you.
-
Do not pass a forklift that is traveling in the same direction.
-
Never drive a forklift up to anyone in front of a fixed object, such as a workbench.
-
Never allow anyone to walk or stand under the elevated forks – even if the forks are not carrying a load.
-
Check that there is adequate clearance under beams, lights, sprinklers, and pipes for the forklift and load to pass.
-
Do not engage in stunt driving or horseplay.
-
Never leave a forklift unattended.
An unattended forklift means that the operator cannot see the machine, or is greater than 25 feet away. Unattended forklifts must be turned off, have the forks on the ground and the brakes set or chocked, if on an incline.
Loading and Unloading the Forklift
Check the load before you pick it up. Secure it as necessary and follow the rules outlined in this Plan.
When you pick up the load:
-
Move squarely into position in front of the load.
-
Position the forks at a width that keeps the load balanced.
-
Drive the forks fully under the load.
-
Tilt the mast backward slightly to stabilize the load, and then lift.
-
Check the destination before you place the load:
-
Is the destination flat and stable or will the load rock, tilt, or lean?
-
Never place heavy loads on top of light loads.
-
Observe maximum stacking quantities and orientation if that information is printed on cartons.
-
Know the load-bearing capacity of your rack or storage loft destination.
-
Check to see if rack legs or support members are bent or disconnected, for the load-bearing capacity of a damaged rack is unknown. Wait until the damaged component has been replaced before loading.
-
When you place the load at its destination:
-
Move squarely into position in front of the rack or stack where the load will be placed.
-
When ready to place the load, tilt the mast to level.
-
Only tilt forward when the load is over the spot where it will be placed.
-
Lower the forks and back away.
-
Visually verify that the load is stable.
Operators are expected to use the proper attachment for handling specific types of loads. The forklift and forks are not to be modified to perform a job for which they are not intended. For special operations, use an attachment designed by the manufacturer for that purpose.
Attachment types include:
-
Push/Pull Clamp
-
Bale Clamp
-
Barrel Clamp
-
Rotating Carriage
-
Turntable Fork Clamp
Driving into a Trailer
Operators may have to drive into trailers at the loading docks. In these cases a dock plate must be used as the bridge for the forklift to safely enter a trailer.
Before entering a trailer, workers are instructed to ensure it is safe to do so. Check for the following conditions:
-
Trucks must be secured to the dock with a vehicle restraint or by chocking the rear tires.
-
Check the dock plates or boards for flaws or damage.
-
Check the bed of the trailer to ensure that it can handle the weight of the forklift and the load.
If a trailer is left at a loading dock without the tractor attached, then use trailer jacks, converters, or blocks to prevent it from up-ending when a forklift drives to the front of the trailer to load or unload.
Lifting and Lowering People
Never allow anyone to be lifted while standing on the forks or on a pallet lifted by the forks. A person lift is available in each building that may require it that meets the specifications of the OSHA standard. When using a forklift to raise a worker to an elevated position, use a platform or structure specifically built for this purpose that meets the following conditions:
-
The platform must have standard guardrails, which include a top rail 36” to 42” above the platform, a middle rail or closed cage, and toe board. It must also prevent contact with chains and shear points on the mast.
-
The platform must be securely attached to the forks, such as by a clamp or chain.
-
Lock or secure the tilt control to prevent the person lift from tilting.
-
A forklift operator must be at the normal operating position when lifting and lowering the platform. The operator must remain on the forklift at all times while a worker is elevated.
-
Do not move the forklift between 2 points when a colleague is on the platform.
Maintenance and Service
Forklifts must be in good operating condition to be safe; OSHA requires that lift trucks must be inspected daily to ensure their safe operation. Shipping and Receiving conducts inspections at the start of each shift and keeps copies of the inspection checklists. When deficiencies or maintenance requirements are noted, these are brought forth to the Warehouse Manager and the unit is repaired. Forklifts have preventive maintenance performed on each lift truck at least once a year or more often as needed.
Recharging Batteries
The forklift battery charging stations are also the off-hours parking locations. When charging or maintaining the batteries, consider the following safety measures.
-
Eye and face protection must be used when charging batteries.
-
All leads and cables must be checked and in good condition.
-
When charging batteries and moving batteries, vent caps must be kept firmly in place to avoid electrolyte splashing.
-
Chargers must be turned off when leads are being connected or disconnected.
-
The battery compartment cover must be left open to dissipate heat and explosive gases.
-
Have materials on hand to neutralize or absorb spilled electrolyte.
-
Ventilation must be adequate to disperse fumes from gassing batteries.
-
Take precautions to prevent open flames, sparks, or electric arcs in battery charging areas.
-
The charging apparatus must be protected from damage.
-
An eyewash fountain/safety shower must be provided at or near (within 10 seconds) of the charging area and be able to dispense clean water for at least 15 minutes.
-
Make sure there is a fire extinguisher nearby.
Changing Propane Tanks
The following are guidelines for safely changing propane tanks on a forklift.
-
Exchange removable cylinders outdoors or in well-ventilated areas, away from sources of ignition.
-
Always protect the valve from any damage.
-
Avoid contact with liquid propane as it can cause frostbite.
-
Wear protective gloves while making or breaking connections.
-
Position the tank so the liquid propane does not come in contact with the relief valve.
-
Make sure the locking pin engages into the cylinder.
-
Make sure the valve is closed tightly.
-
Store the cylinder in an upright position in an area where it can be secured and is protected from being struck.
-
Only workers trained in forklift safety are permitted to change fuel tanks and recharge batteries.
RECORD KEEPING
-
All health and safety training records are to be maintained by EH&S for 3 years.
-
Safety inspection records are to be maintained by EH&S for 3 years.
-
Medical records will be maintained by the HR for the duration of employment plus 30 years.
REFERENCES/RESOURCES
VIDEOS
-
Forklift Safety Tips Video
eLEARNING
DOCUMENTS/LINKS
SUPERVISOR & SAFETY LEADER DEEPER DIVES
-
Article - Loading Dock Distractions
GLOSSARY
Attachments
PIT
Devices (other than conventional forks or load backrest extensions) for a specific use, mounted permanently or temporarily on the elevating mechanism of the truck. Common types include fork extensions, clamps, booms, rams, baskets and personnel platforms.
Authorized employee
PIT, STF
Selected by the employer for that purpose.
CFR
PPE, Chemical, Tools, Electrical, Biosafety, PIT, IIPP, Fire, Emergency, ERT, STF, Vehicle, Violence
Code of Federal Regulations
Capacity
PIT
Used to designate the weight handling ability of a particular truck as equipped.
Dockboard
PIT
A portable or fixed device for spanning the gap or compensating for the differences in height between the loading platform and carrier.
Dockboard (Dock Plate)
STF, Emergency Response, PIT
A portable or fixed device for spanning the gap or compensating for difference in level between loading platforms and carriers.
EH&S
PPE, Chemical, Tools, Electrical, Biosafety, PIT, IIPP, Fire, Emergency, ERT, STF, Vehicle, Violence, Ergo
Environmental Health & Safety (EH&S) has the responsibility of maintaining safety for all workers at Abaxis as outlined in the Health & Safety Policy. Additionally EH&S acts as the conduit for compliance with laws of state & federal regulatory agencies regarding environmental protection, waste disposal, hazard control, and reporting of accidents/incidents at Abaxis.
Emergency
PPE, Chemical, Tools, Electrical, Biosafety, PIT, IIPP, Fire, Emergency, ERT, STF, Vehicle, Violence
1) Any potential occurrence such as, but not limited to, equipment failure, rupture of containers, or failure of control equipment, which may or does result in a release of a hazardous substance into the workplace.
2) An unforeseen combination of circumstances or the resulting state that increases the threat to health, life, or property and calls for immediate action.
Forklift
PIT
A self-loading truck equipped with load carriage and forks for transporting and tiering loads.
Forks
PIT
Horizontal tine-like projections, normally suspended from the carriage that engage and support loads.