HAZARD COMMUNICATION
POLICY & PURPOSE
It is Zoetis Union City policy to provide information to colleagues and visitors regarding hazardous materials that are used at each facility, and to comply with applicable requirements under the Cal/OSHA Hazard Communication (HazCom) Standard.

The purpose of this HazCom Plan is to inform colleagues of the hazards, and safe handling practices, for chemicals used and stored in our facilities. This Plan also establishes the criteria for the information that is provided in Zoetis Union City Safety Data Sheets (SDS). This Plan intends to comply with both the HazCom Standard (Title 8 Code of California Regulations, Section 5194) and Proposition 65 requirements.
Sections of this program include: (click on each button for more detail or use switch to open/close all)
RESPONSIBILITIES
Under the provisions of the HazCom Standard, employers are responsible for informing colleagues of the hazards and the identities of workplace chemicals to which they are exposed.
FACILITIES
Facilities is responsible for installing appropriate signage to warn workers of potential hazards at Zoetis Union City.
THE SAFETY COMMITTEE and EH&S
The Safety Committee and EH&S are responsible for identifying new risks and providing appropriate signage to Facilities. EH&S maintains Safety Data Sheets for all Hazardous Chemicals at Zoetis Union City.
SUPERVISORS
Supervisors are responsible for training colleagues about hazards in their work areas and pointing out hazard signage, and warning labels, as well as reviewing new Safety Data Sheets with colleagues if new hazards are presented.
Supervisors and managers are required to conduct hazard awareness training when new procedures are implemented, when new equipment that uses hazardous chemicals is introduced to the workplace, and when new chemicals are brought on site for the first time. Hazard warning information may also be provided through emails to affected colleagues or in short work-site training sessions that focus on a particular chemical or process.
COLLEAGUES
Colleagues are responsible with complying with all hazard warning signage and for actively seeking out information through Safety Data Sheets on hazardous materials they may be working with.
TRAINING
Colleagues who handle, or work in locations where chemicals are handled and stored, are trained on this Plan after they begin working at Zoetis Union City. New Hire Safety Orientation provides training in how to read an SDS and where they are located in the company.
All colleagues who are affected by this Plan are required to read this chapter in the Safety Manual.
Non-Routine Tasks
On those occasions when colleagues are asked to perform a non-routine task involving chemicals, the colleague is then provided with hazard information regarding the chemicals involved. This information includes the following:
-
Specific chemical hazards.
-
Control measures and safety provisions that have been implemented by the company to prevent exposures or contamination to the chemicals being used.
-
Required protective/safety measures.
PROGRAM REQUIREMENTS
Chemical Inventory
A physical chemical inventory is collected periodically and establishes the list of chemicals for which SDSs are required. According to the OSHA Standard, Zoetis Union City must have an SDS for every chemical in the inventory, including industrial chemicals such as bleach, parts cleaners, and machine lubricants.
A chemical inventory is also the basis for several regulatory reporting requirements related to local agencies for environmental compliance, building permits, and other potential submissions. The chemical inventory is maintained in the EH&S files.
Proposition 65 Compliance
Proposition 65, also known as the Safe Drinking Water and Toxic Enforcement Act of 1986, requires that companies with listed chemicals post warnings to the public and specific warnings to colleagues who may be exposed to these chemicals.
To comply with this regulation, Zoetis Union City posts hazard awareness signs at entrances to its buildings.
In 2016, the California Office of Environmental Health Hazard Assessment (OEHHA) launched a new website, www.P65Warnings.ca.gov, to provide the public with more information on chemicals, products, and locations associated with Proposition 65 warnings. The website is part of the state’s effort to provide Californians with more useful information on chemicals they are being exposed to and ways to protect themselves.
People who read Proposition 65 warnings and want to learn more can go to the website to find additional information about chemicals and best practices for reducing or eliminating exposures. The website contains fact sheets about Proposition 65 chemicals and specific types of exposure, such as from furniture products or enclosed parking facilities. It also answers frequently asked questions about Proposition 65 and includes a glossary of Proposition 65 terms.
Zoetis Union City is also required to provide a clear warning to colleagues who handle listed chemicals by one of the following methods:
-
A warning that appears on the label that is read and understood by colleagues or other individuals prior to its use.
-
A warning that is posted in the workplace in a conspicuous place that makes it likely to be read and understood by workers.
-
A warning to colleagues who handle a listed chemical that complies with the Hazard Communication Standard.


Safety Data Sheets (formerly Material Safety Data Sheets)
SDSs are documents which are produced by chemical manufacturers and distributors that state the physical and chemical properties of the product, the physical and health hazards, and precautions for safe handling and use. The chemical inventory is the basis for ensuring that a corresponding SDS is on file.
-
Each chemical that is handled or used in the workplace is required to have a corresponding SDS
-
Colleagues must have access to the SDSs at all times of the workday and during all work shifts..
Colleagues may also download an app for their smartphones from the Apple Store or Google Play. Search for MSDS Online. Once installed, click on "Don't have a username or password". The app will allow you to scan this QR Code and sign into the Zoetis Union City SDS Binder.

Supervisor's Note
All chemicals at Zoetis Union City must have accompanying SDS upon delivery, or have an internal SDS on file if it is a validated material (internal SDS can be obtained from the Abaxis website). SDSs may be received with the delivery or mailed to the EH&S department. SDSs can be obtained by asking the manufacturer to fax a copy to the requester or from a manufacturer’s website.
When chemicals that are not listed in the current inventory are purchased, or chemicals are not purchased through Zoetis Union City purchasing department, the requester must provide the EH&S department with the SDS and the location where the chemical will be used, the volume of the container, and number of containers, and EH&S will ensure that the SDS is filed in the SDS library.
Businesses that have multiple workplaces must have SDSs available for those chemicals that are used and stored at each building. Hard copies of SDSs are kept in binders in the main hallway outside the Rotor Manufacturing gowning room in Building 1. These are available for viewing at all times during the day.
Abaxis Product SDSs
Abaxis produces SDSs for their products. These must meet the GHS standard information requirements. Each SDS must provide hazard information specific to the specific product.
Manufacturers are responsible under this Standard to evaluate the hazards using scientifically proven hazard determination methods, or by referencing literature sources acceptable to OSHA in determining the hazards.
Abaxis SDSs are available for review on the company’s website and network drive. They are distributed to customers as requested.
FOR SDS Preparers Only
OSHA requires that the SDS preparers provide specific minimum information as detailed in Appendix D of 29 CFR 1910.1200. The SDS preparers may also include additional information in various section(s).
The required format for SDSs is defined in the Hazard Communication Standard (HCS) (29 CFR 1910.1200(g)), revised in 2012 and must include the following sections:
-
Section 1: Identification
-
Section 2: Hazard(s) Identification
-
Section 3: Composition/information on Ingredients
-
Section 4:First-Aid Measures
-
Section 5: Fire-Fighting Measures
-
Section 6: Accidental Release Measures
-
Section 7: Handling and Storage
-
Section 8: Exposure Controls/Personal Protection
-
Section 9: Physical and Chemical Properties
-
Section 10: Stability and Reactivity
-
Section 11: Toxicological Information
-
Section 12: Ecological Information
-
Section 13: Disposal Considerations
-
Section 14: Transport Information
-
Section 15: Regulatory Information
-
Section 16: Other Information
Trade Secrets
Manufacturers can protect trade secrets in a product or formulation by excluding this information on the SDS, as long as it meets the following requirements.
-
The SDS must state that the specific identity of the chemical mixture is being withheld as a trade secret.
-
Trade secret information must be released in both emergency and non-emergency circumstances, with a written request. Excluded chemical information must be honored unless the manufacturer does the following:
-
Explains why the disclosure of the specific chemical identity is essential, and
-
Describes the procedures by which the disclosed information will be kept confidential.
-
According to Cal/OSHA, a chemical or formulation cannot be called a trade secret if its identity is already discoverable through qualitative laboratory analysis.
Chemical Warning Labels
OSHA has adopted new hazardous chemical labeling requirements as a part of its recent revision of the Hazard Communication Standard, 29 CFR 1910.1200 (HCS), bringing it into alignment with the United Nations’ Globally Harmonized System of Classification and Labeling of Chemicals (GHS).
The revised standard requires that information about chemical hazard be conveyed on labels using quick visual notations to alert the user, providing immediate recognition of the hazards. Labels must also provide instruction on how to handle the chemical so that chemical users are informed about how to protect themselves. This includes manufacturer containers that are missing hazard information, as well as containers of formulations made and used in Zoetis Union City work areas.
At a minimum, all chemical containers must have labels that contain the following information:

GHS PICTOGRAMS
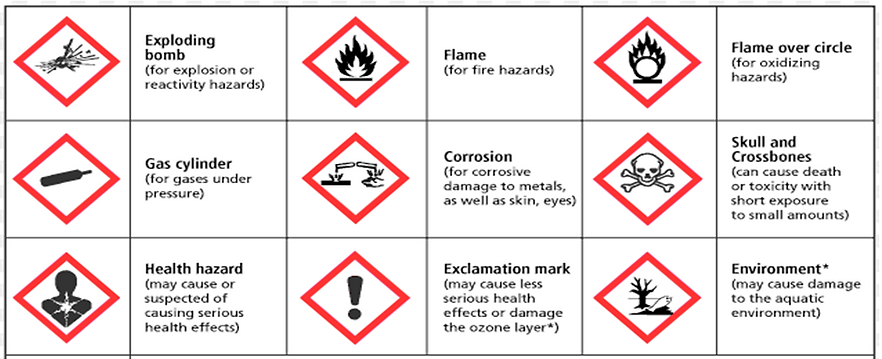
Additional requirements for chemical labeling include the following:
-
Existing labels on incoming containers of hazardous substances must not be removed or intentionally defaced
-
Hazard warning labels must be legible, in English, and prominently displayed on the container.
If a lab has bottles of stock solutions, all of a similarly low hazard class, it may be more practical to label a common secondary container with one hazard warning label.
Common types of hazard warning labels include those with the four-part National Fire Protection Association (NFPA) diamond or similar labels using a color-coded numerical ranking for hazards. For containers with only one hazardous material, such as Diluent H, then a single hazard warning is necessary (i.e., Toxic).
Other Hazard Warnings and Hazard Information
Zoetis Union City communicates hazard information and warnings by several other methods aside from container labels and SDSs. These satisfy a number of safety concerns, including:
-
Signage
-
Pipe & Process Labeling
Signage
-
Signs indicating the location of safety eyewash fountains, fire extinguisher, AED's & first aid kits
-
Appropriately labeled cabinets for storing flammable or corrosive chemicals
-
Door signs on entrances to each work area that display :
- The NFPA diamond applicable to the highest hazard materials in the work area, including “select carcinogens” if they are present
-
The highest hazard chemicals used in that location
-
The biosafety level for that location, if applicable
-
Required personal protective equipment (PPE)
-
Emergency 24-hour contact information
How to Read a National Fire Protection Agency (NFPA) Diamond

Example of a Door Sign

Pipe and Process Labeling
Above ground piping systems that are used to transport gases, vapors, liquids, semi-liquids shall be identified with the following information. These are found on pipes used to service lyophilizers, gas systems such as compressed air or nitrogen, and process piping for refrigeration units.
-
Color coding, or colored bands, with the name or abbreviation of the material inside the pipe.
-
The direction of flow in the pipe.
-
Tags that name the material inside the pipe should be fastened securely to the system, either on or near the valve.
New systems or processes will be required to label process piping according to this standard, and building codes, where applicable.
RECORD KEEPING
Safety Data Sheets (SDSs) are kept on site for 30 years.
REFERENCES/RESOURCES
VIDEOS
eLEARNING
DOCUMENTS/WEBLINKS
SUPERVISORS & SAFETY LEADERS DEEPER DIVE
GLOSSARY
Emergency situation
BBP, Biosafety, Chemical Hygiene, HazCom, Emergency Response, ERT
Any occurrence such as, but not limited to, equipment failure, rupture of containers, or failure of control equipment that may or does result in an uncontrolled significant release of an airborne contaminant.
Employee exposure
BBP, Biosafety, Chemical Hygiene, HazCom
Exposure to a concentration of an airborne contaminant that would occur if the employee were not using respiratory protection.
Engineering Controls
BBP, Biosafety, Chemical Hygiene, HazCom
Controls may include working in fume hoods, enclosures, or modify work processes/equipment to decrease the exposure of hazardous atmospheres.
Environmental Air Monitoring
Chemical Hygiene, HazCom
The process of measuring the airborne fiber concentration within a specific volume of air.
Explosive
Chemical Hygiene, Fire, HazCom, Emergency Response
1) A substance that causes a sudden, almost instantaneous release of pressure, gas, and heat when subjected to sudden shock, pressure, or high temperature
2) A solid or liquid chemical which, by itself, can chemically react to produce gases at such a temperature and pressure and at such a speed as to cause damage to the surroundings. Pyrotechnic chemicals are included even when they do not evolve gases..
Exposure or exposed
BBP, Biosafety, Chemical Hygiene, HazCom
Any situation arising from work operation where an employee may ingest, inhale, absorb through the skin or eyes, or otherwise come into contact with a hazardous substance.
Eyewash
Chemical Hygiene, HazCom, BBP, Biosafety, Emergency Response, ERT
A device used to irrigate and flush the eyes.
Flammable
Chemical Hygiene, HazCom, Fire, Emergency Response
A substance that falls into one of the following categories: 1) Flammable gas means a gas having a flammable range with air at 20C (68F)and a standard pressure of 101.3 kPa (14.7 psi). 2) Flammable liquid means a liquid having a flash point of not more than 93C(199.4F). 3) Flammable solid means a solid which is a readily combustible solid, or which may cause or contribute to fire through friction. Readily combustible solids are powdered, granular, or pasty substances which can be easily ignited by brief contact with an ignition source, such as a burning match, and for which flame spreads rapidly. 4) Flammable aerosol means an aerosol containing any flammable materials. An aerosol is defined as a non-refillable receptacle containing a gas compressed, liquefied, or dissolved under pressure, and fitted with a release device allowing the contents to be ejected either as suspended particles in a gas, or as a foam, paste, powder, liquid, or gas.
Flammable Liquid
Chemical Hygiene, HazCom, Fire, Emergency Response
Any liquid that has a closed-cup flash point below 100F (37.8C).
Flash Point
Chemical Hygiene, HazCom, Fire, Emergency Response
The minimum temperature of a liquid at which sufficient vapor is given off to form an ignitable mixture with air, near the surface of the liquid or within the vessel used.