INJURY & ILLNESS PREVENTION PROGRAM (I2P2)
Colleagues are expected to know their responsibilities for safety at work and to apply the principles and practices by which they are trained. While safe work practices apply to all work areas, this Injury and Illness Prevention Program is intended to be flexible and dynamic and subject to revision as the company grows and changes.
This Program is designed to comply with the requirements of the California Occupational Safety and Health Administration (Cal/OSHA) requirements as stated in the Cal/OSHA standard (Title 8 Code of California Regulations, Section 3203)
Sections of this program include: (click on each button for more detail or use switch to open/close all)
HEALTH & SAFETY POLICY
Union City management is committed to creating a safe and healthful work environment for our colleagues (regular & contingent), contractors and our community.
We accomplish this goal by careful work-site analysis & control, hazard prevention programs, and active colleague participation & awareness through regular safety & health training.
RESPONSIBILITY
Program Administrator has the authority and responsibility for implementing the provisions of this program for Union City site
.
All managers and supervisors are responsible for implementing and maintaining the I2P2 in their work areas and for answering worker questions about the I2P2.
COMPLIANCE
Management is responsible for ensuring that all safety and health policies and procedures are clearly communicated and understood by all workers. Managers and supervisors are expected to enforce the rules fairly and uniformly.
All colleagues are responsible for using safe work practices, for following all directives, policies and procedures, and for assisting in maintaining a safe work environment.
Our system for ensuring that all colleagues comply with the rules and maintain a safe work environment includes:
-
Informing colleagues of the provisions of our I2P2.
-
Evaluating the safety performance of all workers;
-
Recognizing workers who perform safe and healthful work practices;
-
Providing training to workers whose safety performance is deficient;
-
Referring workers that fail to comply with safe and healthful work practices to Human Resources.
COMMUNICATION
We recognize that open, two-way communication between management and colleagues on health and safety issues is essential to an injury-free, productive workplace. The following system of communication is designed to facilitate a continuous flow of safety and health information between management and staff in a form that is readily understandable and consists of one or more of the following items:
-
New hire orientation including a discussion of safety and health policies and procedures.
-
Review of our I2P2.
-
Workplace safety and health training programs.
-
Regularly scheduled safety meetings.
-
Effective communication of safety and health concerns between colleagues and supervisors, including translation where appropriate.
-
Posted or distributed safety information.
-
Safety suggestion box
-
A system for workers to anonymously inform management about workplace hazards.
As a method of further accountability we have a Safety Committee that:
-
meets regularly,
-
prepares written records of the safety committees meetings,
-
reviews results of the periodic scheduled inspections,
-
reviews investigations of accidents and exposures and makes suggestions to management for the prevention of future incidents,
-
reviews investigations of alleged hazardous conditions,
-
and submits recommendations to assist in the evaluation of colleague safety suggestions.
HAZARD ASSESSMENT
Periodic inspections to identify and evaluate workplace hazards shall be performed by the following competent observers) in the following areas of our workplace:
Periodic inspections are performed according to the following schedule:
-
Monthly or
-
When we initially established our I2P2;
-
When new substances, processes, procedures or equipment which present potential new hazards are introduced into our workplace;
-
When new, previously unidentified hazards are recognized;
-
When occupational injuries and illnesses occur;
-
When we hire and/or reassign permanent or intermittent workers to processes, operations, or tasks for which a hazard evaluation has not been previously conducted; and
-
Whenever workplace conditions warrant an inspection.
Periodic inspections consist of identification and evaluation of workplace hazards.
REPORTING OF OCCUPATIONAL INJURIES AND ILLNESSES/INCIDENTS
Colleagues are required to report all work-related injuries, illnesses, and/or incidents that result in property damage and near-miss incidents to their supervisor, to Human Resources, or to EH&S either by using the Workplace Incident Report (WIR) form, by sending an electronic report through our weblink or through direct verbal communication with their manager/supervisor or appropriate delegate.
Serious or life threatening injuries should receive immediate treatment prior to concern for completing any required paperwork or conducting a root cause investigation.
The colleague's supervisor is responsible for assisting them to completing the WIR as well as for initiating the Incident Investigation Report (IIR) Form according to the instructions on the form.
The form is then processed according to Flowchart 1.
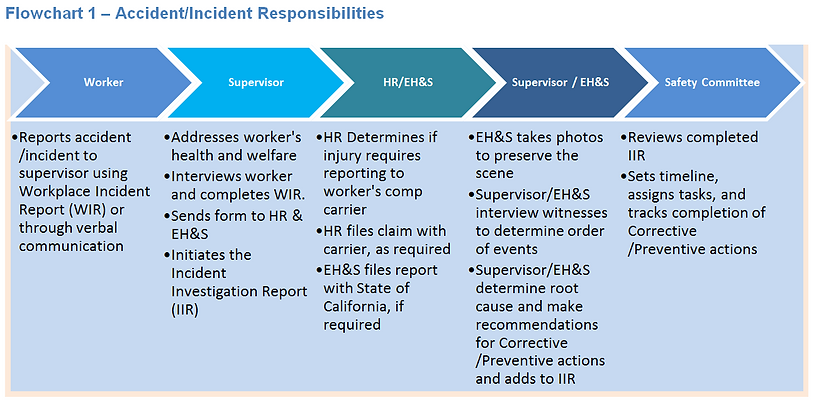
Accident/Incident Investigations
Procedures for investigating workplace accidents and hazardous substance exposures include:
-
Visiting the accident scene as soon as possible;
-
Interviewing injured colleagues and witnesses;
-
Examining the workplace for factors associated with the accident/exposure;
-
Determining the cause of the accident/exposure;
-
Taking corrective action to prevent the accident/exposure from reoccurring; and
-
Recording the findings and corrective actions taken.
This is all documented on the Incident Investigation Report form.
HAZARD CORRECTION
Unsafe or unhealthy work conditions, practices or procedures shall be corrected in a timely manner based on the severity of the hazards. Hazards shall be corrected according to the following procedures:
-
When observed or discovered;
-
When an imminent hazard exists which cannot be immediately abated without endangering colleague(s) and/or property, we will remove all exposed colleagues from the area except those necessary to correct the existing condition. Collegues necessary to correct the hazardous condition shall be provided with the necessary protection; and
-
All such actions taken and dates they are completed shall be documented on the appropriate forms.
TRAINING
All colleagues, including managers and supervisors, shall have training and instruction on general and job-specific safety and health practices. Training and instruction shall be provided as follows:
-
When the I2P2 is first established;
-
To all new colleagues
-
To all colleagues given new job assignments for which training has not previously provided;
-
Whenever new substances, processes, procedures or equipment are introduced to the workplace and represent a new hazard;
-
Whenever Union City site is made aware of a new or previously unrecognized hazard;
-
To supervisors to familiarize them with the safety and health hazards to which colleagues under their immediate direction and control may be exposed; and
-
To all colleagues with respect to hazards specific to their job assignment.
Workplace safety and health practices include, but are not limited to, the following:
-
Explanation of the Zoetis Union City I2P2, emergency action plan and fire prevention plan, and measures for reporting any unsafe conditions, work practices, injuries and when additional instruction is needed.
-
Use of appropriate clothing, including gloves, footwear, and personal protective equipment.
-
Information about chemical hazards to which colleagues could be exposed and other hazard communication program information.
-
Availability of toilet, hand-washing and drinking water facilities.
-
Provisions for medical services and first aid including emergency procedures.
In addition, we provide specific instructions to all workers regarding hazards unique to their job assignment, to the extent that such information was not already covered in other training.
RECORDKEEPING
We have taken the following steps to implement and maintain our I2P2:
-
Records of hazard assessment inspections, including the person(s) or persons conducting the inspection, the unsafe conditions and work practices that have been identified and the action taken to correct the identified unsafe conditions and work practices, are recorded on a hazard assessment and correction form; and
-
Documentation of safety and health training for each worker, including the colleague's name or other identifier, training dates, type(s) of training, and training providers are recorded on a Training and Instruction Form (SOP-0008-01).
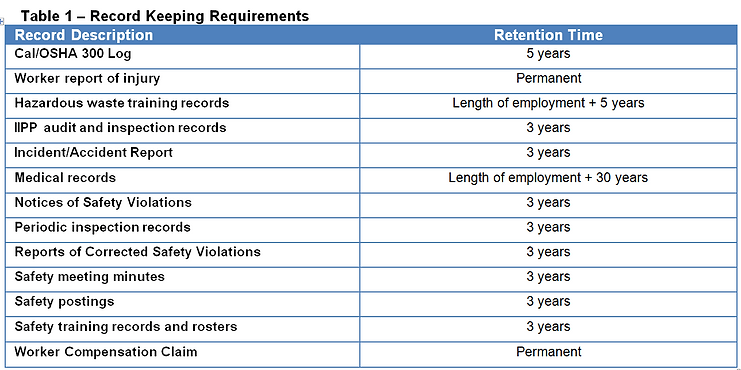
REFERENCES/RESOURCES
DOCUMENTS/WEBLINKS
FORMS/LINKS
VIDEOS
eLEARNING
SUPERVISOR & SAFETY LEADER DEEPER DIVES
-
Article - Ten Most Asked Questions About OSHA Inspection Process
-
Article - The Safety Experience
-
Article - Fatigue - You're More than Just Tired!
-
Infographic - Workplace Injuries
GLOSSARY
Industrial Stairs
Fire, IIPP, STF, Emergency Respnose
A series of steps leading from one level or floor to another, or leading to platforms, pits, boiler rooms, crossovers, or around machinery, tanks, and other equipment. A series of steps and landings having three or more risers constitutes an industrial stair or stairway.
Landing
IIPP, STF
An extended step or platform breaking a continuous run of steps or ramps.
Licensed Healthcare Professional
PPE, Chemical, Tools, Electrical, Biosafety, PIT, IIPP, Fire, Emergency, ERT, STF, Vehicle, Violence
A person whose licensed scope of practice includes an activity which this section requires to be performed by a licensed healthcare professional.
NIH
PPE, Chemical, Tools, Electrical, Biosafety, PIT, IIPP, Fire, Emergency, ERT, STF, Vehicle, Violence
National Institute of Health
NIOSH
PPE, Chemical, Tools, Electrical, Biosafety, PIT, IIPP, Fire, Emergency, ERT, STF, Vehicle, Violence
The Director of the National Institute for Occupational Safety and Health, U.S. Department of Health and Human Services, or designated representative.
Panic Hardware
STF, Emergency Response, IIPP
A bar which extends not less than one-half the width of each door leaf, not less than 30 nor more than 44 inches above the floor, which will unlatch the door when a force to the bar not to exceed 15 pounds is applied in the direction of exit travel.
Personal Protective Equipment
PPE, Chemical, Tools, Electrical, Biosafety, PIT, IIPP, Fire, Emergency, ERT, STF, Vehicle, Violence
1) Specialized clothing or equipment worn or used by an employee for protection against a hazard. General work clothes (e.g., uniforms, pants, shirts or blouses) not intended to function as protection against a hazard are not considered to be personal protective equipment.2) Safety devices and safe guards worn to eliminate or minimize the hazard to an individual's head, eye, body, hand, foot, and extremities. Examples of PPE include laboratory coats, eye/face protection (e.g., safety glasses, goggles and face shield), gloves (e.g., chemical-resistant, thermal protection, cut-resistant), hearing protectors (e.g., earplugs, ear muffs), respirators (e.g., N95 disposable respirator, half-face negative-pressure respirator with appropriate filters/cartridges), hard hats, and steel toed shoes.
Physical hazard
Chemical Hygiene, Hazcom, IIPP, Electrical, Tool
1) A chemical that is classified as posing one of the following hazardous effects: explosive; flammable (gases, aerosols, liquids, or solids); oxidizer (liquid, solid or gas); self-reactive; pyrophoric (liquid or solid); self-heating; organic peroxide; corrosive to metal; gas under pressure; or in contact with water emits flammable gas. Detailed explanations of physical hazards classifications can be found online.
2) Substances, equipment, or activities that pose potential threat to physical safety. Examples of physical hazards include, but are not limited to: extreme pressures, temperature extremes, radiation (ionizing and non-ionizing radiation), noise, and flying hazards due to machining equipment.
Physician or other licensed health care professional (PLHCP)
PPE, Chemical, Tools, Electrical, Biosafety, PIT, IIPP, Fire, Emergency, ERT, STF, Vehicle, Violence
an individual whose legally permitted scope or practice (i.e., license, registration, or certification) allows him or her to independently provide, or be delegated the responsibility to provide, some or all of the health care services required by Sections 2.4 and 10.
Qualified Person, Attendant or Operator
IIPP
A person designated by the employer who by reason of his training and experience has demonstrated his ability to safely perform his duties and, where required, is properly licensed in accordance with federal, state, or local laws and regulations.